14/06/2021
The latest industrial revolution—Industry 4.0, transforming manufacturing operations by making best use of connected data—has a problem: there’s too much data to look at.
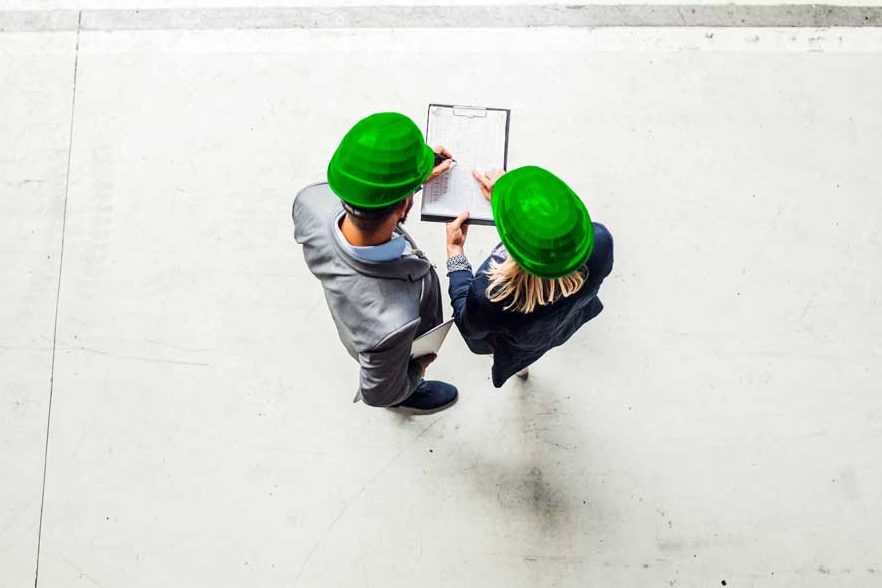
Even the simplest production system has thousands of numbers you could gather with a Manufacturing Execution System (MES). Volumes and capacities; pressures and temperatures; calibration and tolerances. For enterprise-scale operations, where a thousand units might be an everyday run, there may be a case for collecting every data point—and they have the resources to do so. But for smaller manufacturers, watching every last measure and metric isn’t just redundant—it may be actively harmful.
After all, some data points in your business matter more than others. And in the SME space, success depends on those: the business-critical bits that make the biggest difference.
90% of the capabilities of an enterprise MES might be useless to you. Which means a big-name MES might not be the right tool for the job—any more than you need an articulated lorry to get your weekly shopping home.
Let’s look at how a right-sized MES makes more sense for the SME, and how you can get your hands on one that fits.
Shifting paradigms, endless opportunities
The opportunities of Industry 4.0 today are much like those the Internet opened up a generation ago. For the same reason. A basic PC on a desk is useful—to one person. Connect it to other PCs, and it can share data, becoming useful to a whole team, whilst connecting it to billions of others worldwide brings you the infinite resources of SaaS, cloud computing, datacentres, and web services.
When you connect things together, you increase value for everyone (known as Metcalfe’s Law.) But just as online banking and productivity apps share space with time-munching Facebook and Instagram, the major players in MES try to be all things to all people. Monolithic solutions with vast feature sets, needing armies of consultants to tweak and nudge into function. In short: industrial-scale MES take a long time and are very expensive. (A large implementation can cost millions.) So what’s to be done?
Benefitting from bespoke
For a smaller specialist manufacturer, an off-the-shelf MES is overkill. You’ll spend more time maintaining it than getting value from it, and resources that could be going into continuous improvement will sink into a software system — and wasn’t an MES supposed to save resources?
Here’s the magic word: bespoke. An MES individually designed for your SME, joining together the data that gives you competitive advantage. If the ‘bespoke’ word reminds you of £60,000 jewellery and celebrity architects, think again. A bespoke MES is custom-designed for your precise needs … but the components that go into it are standard. Giving you the benefit of a custom solution, but the cost advantages of using tested and proven parts.
Making the MES make sense
Getronics’ Paul Ferguson offers an analogy: an MES for SMEs is like a smartwatch. It gathers key metrics—heart rate, steps taken, how attractive you look in Spandex—and reports the ones that matter, so you can take corrective action if any trend incorrectly. (OK, he’s joking about the attractiveness one.)
That’s what makes a smartwatch useful: it’s compact, easy to use, and customized for you.
Of course, a full-featured medical clinic has wardrobe-sized scanners and sensors that do much more—but you wouldn’t want to carry them on your daily run. A smartwatch isn’t oversized; it’s right-sized.
So if you want an MES that works for your SME, think like a smartwatch. Musashi Spain Villalba did.
The fortunes of Musashi Spain Villaba
Musashi Spain Villalba, the Spain-based metallurgist is part of Japan’s Musashi Group, providing the key competency of cold-forming. Like many established companies, however, its production controls had fallen behind the times, with a lot of manual inputs creating traceability issues along the value chain.
Getronics’ solution for Musashi in Spain connected processes across the business, from downloading work orders from its ERP to automatic capture of machine activity that enabled easier resolution of stoppages and incidents. Even workers’ bonuses were included, calculated from actual data gathered in real-time—incentivising accountability!
Note that all the components were available already: the creative customisation was in how Getronics configured each module to work together in the context of the manufacturer’s processes. That’s what made it bespoke—and what made it perform.
The results? Quality issues falling and the improvement of effective execution times across all processes.
Conclusion
That’s the Getronics view on MES: adaptable and flexible readymade applications, joined together into an end-to-end solution rightsized for your business. As with other trends in Industry 4.0, the value isn’t just in the machines—it’s in the data connections between them.
Intrigued by what this approach could do for your shopfloor production environment? Let’s talk.